

Because gear calculations require many complex formulas related to strengths and sizes, traditional gear design.
AUTOCAD GEAR GENERATOR SOFTWARE
In any case, in modern context, it is not usually necessary to draw the detail of a gear in an engineering drawing as it will be specified elsewhere.Īlso be aware that for meshing spur gears the dimensions and profiles of the teeth must be the same regardless of the diameter of the gear ie you cant just draw a template gear of one size and scale it to give different rations. The gear calculator is a comprehensive software which, after inputting various parameters related to gear calculations, computes on-line automatically gear sizes, strengths, working forces, tooth forms, backlash conversions, etc. AutoCad probably has a feature to draw the teeth for you based on this information but I don't know for sure. Note that in the module system you need to work out your gear rations by number of teeth, you can't just have arbitrary diameters as for obvious reasons you can't have fractions of teeth on meshing spur gears.įor assembly drawings it is common to draw meshing gears as circles of the appropriate PCD and use a note to specify the module. During generation, a tool runout can be developed. The cylindrical gears can be created as a single part or directly on an existing part. The calculation of the 3D tooth form is conducted according to a mathematical simulation of the manufacturing and rolling process. Although in practice this often means picking an off the-shelf gear set rather than getting them manufactured as stock gears will cover almost all requirements. The gears include the accurate tooth form. This leaves the designer to specify thing like the thickness of the gear (which determines its torque capacity) as well as the arrangements for fixing it to a shaft.

This means that the fiddly calculations of tooth profile, clearances etc are covered by the standard so you don't have to reinvent the wheel every time you design a part with gears in it.
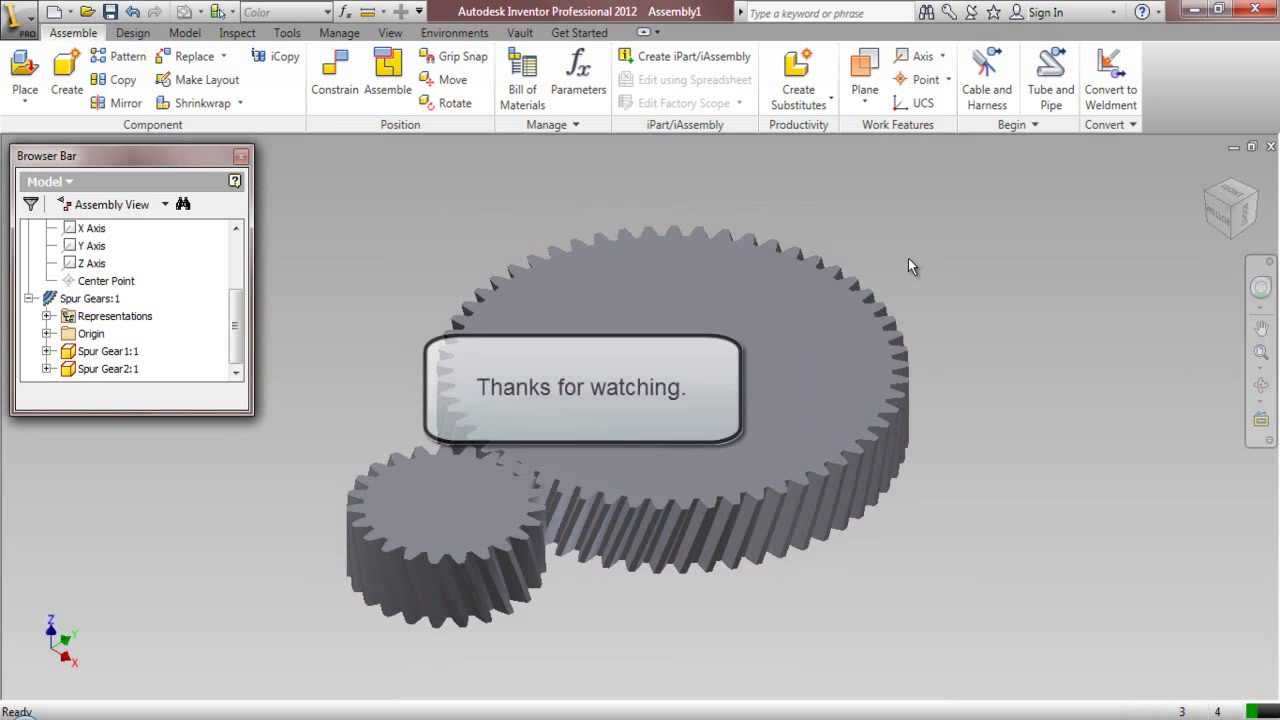
This specifics gears according to pitch circle diameter and number of teeth (the module number is the ratio between the two). Metric gears are usually designed to the module system. Gear design from scratch is a fairly major process in itself and so the vast majority of gears are made to standardised tooth profiles.
